This video shows how packing pressure influences the dimensions of the mold.
Plastic melt has a higher volume compared to solid unmolten plastic. Consider a mold cavity of dimension A. Refer to the video above. If it is filled with melt it will have less number of molecules compared to if it was solid unmolten plastic. As the melt cools down, it will occupy less space because of the shrinkage resulting in a part with a dimension smaller than the cavity dimension. Let us call value of the value of this dimension as B. During the shrinkage if more plastic is added (packing phase) and the added molecules reduce the inter molecular distance restricting the molecules to shrink to the previous levels. The part will therefore have a larger dimension and will be B which is greater than A. If the pressure is further increased during the packing even more plastic is added further reducing the inter molecular distance and therefore the shrinkage resulting in C which is greater than B.
So technically speaking, the part dimension did not increase but ‘The part shrinkage was reduced with an increase of packing pressure’.
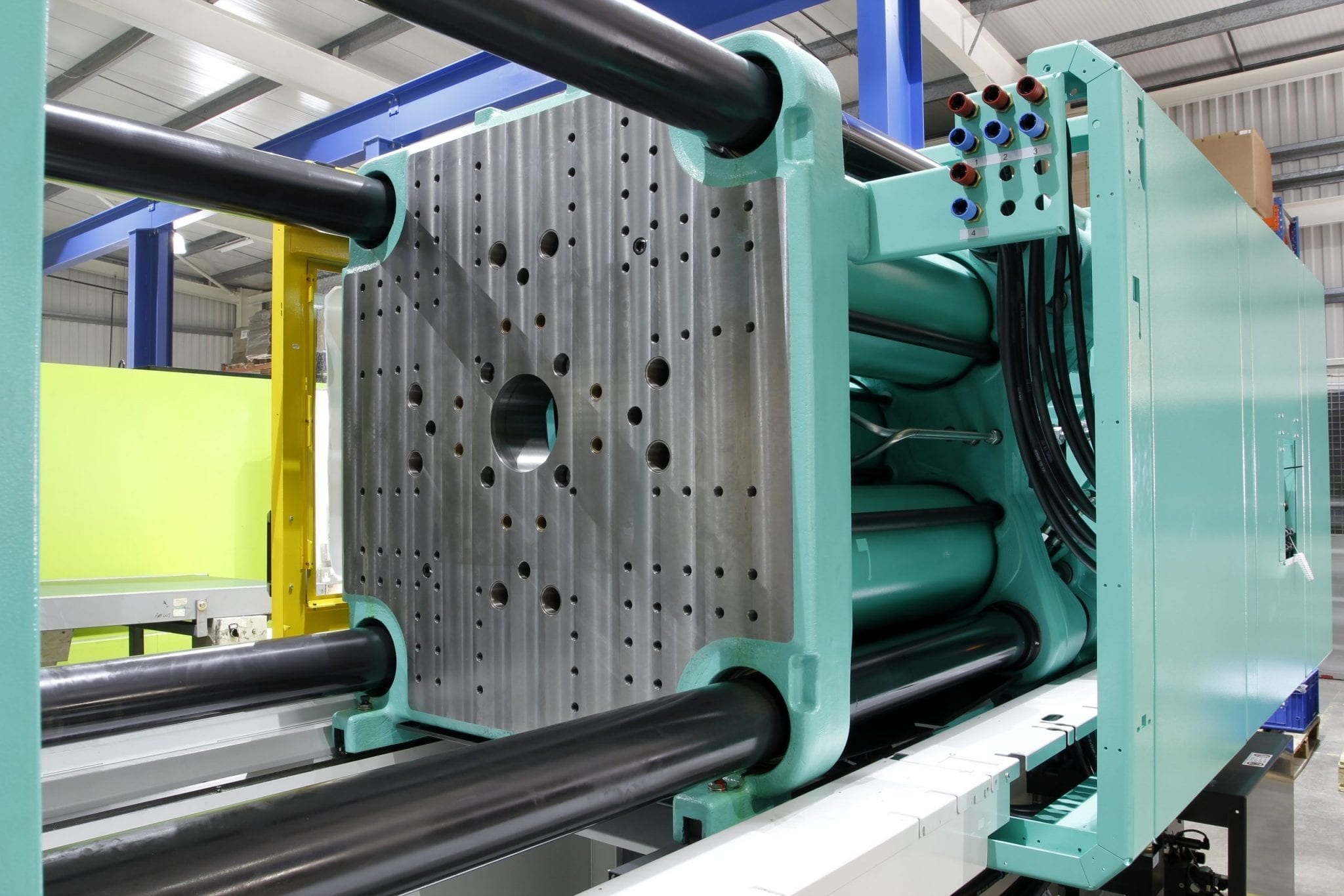