When I teach the concept of Back Pressure in my seminars almost always one of the attendees will say ‘Increasing back pressure will increase the melt temperature’. That is absolutely true! However, there are a few things we must understand about back pressure. One should only use the minimum needed and never to fix dimensional problems. Read on.
So what is back pressure? As the screw rotates to pick up the plastic for the next shot, the accumulated material pushes the screw back. When the screw reaches the shot size, the screw rotation stops. The volume of the barrel that is filled with the plastic should be equal to the volume of the runners plus the cavities in the mold. (Ignore cushion for now.) Back pressure is the pressure applied to the back of the screw to compress the melt to a consistent volume. Since Part Weight = Melt density X Volume, consistency from shot to shot can only be achieved when the melt density is consistent from shot to shot. Since volume is fixed it plays no role in consistency. The back pressure maintains this shot to shot melt density. Increasing it to more than required will only make the plastic slip on the screw, increasing shear and therefore the melt temperature. A certain percentage of the heat is generated, and must be generated by shear but it should be capped off once the balance between the barrel heats and the shear heats is reached.
Back pressure also serves the purpose of compressing the melt to remove any volatiles that will get into the melt and cause splay. Again, a minimum amount of back pressure must be used to get rid of the splay.
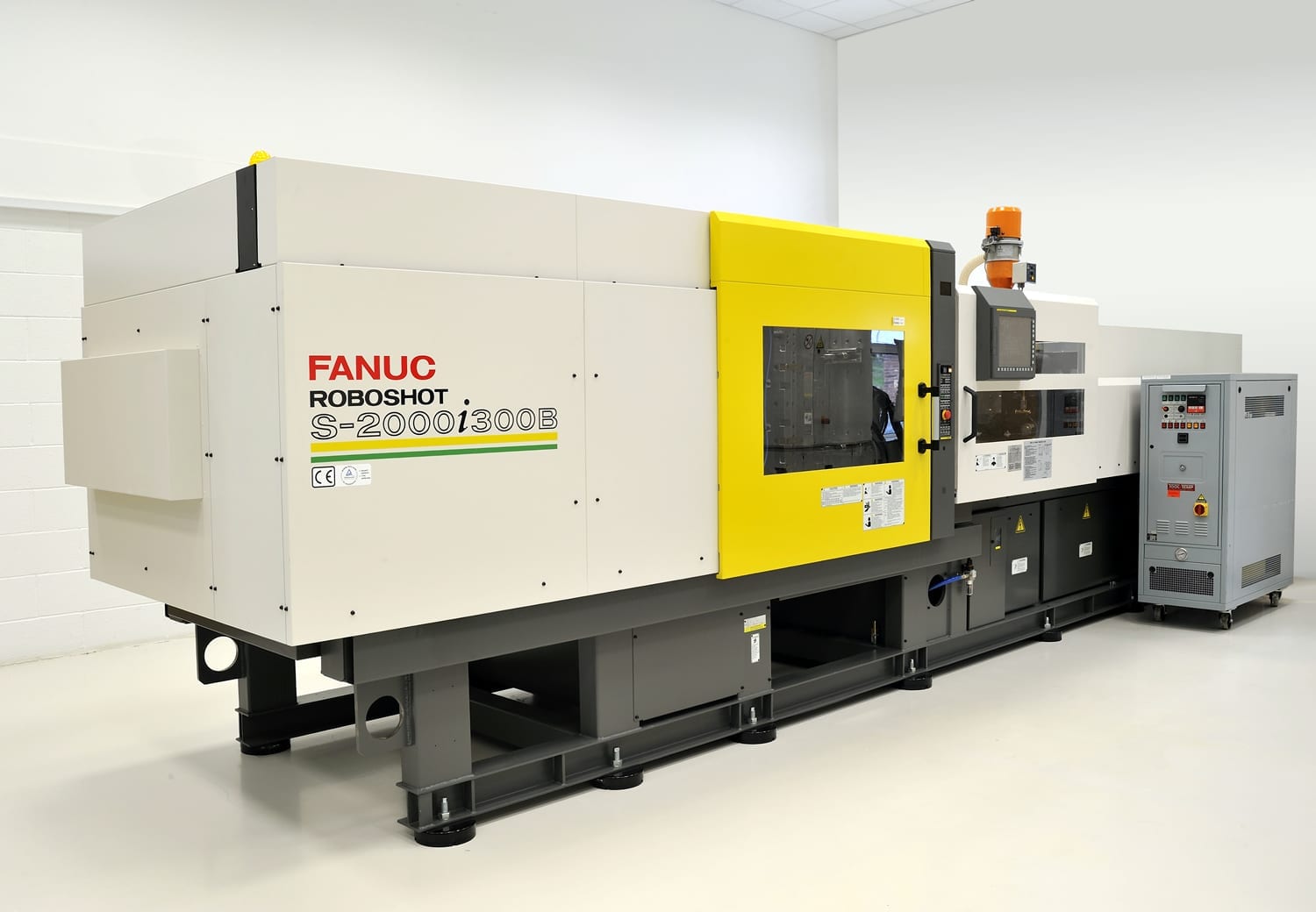