One of my customers called me since he was having issues with one of their new molds and parts. He had visited the mold maker for first shots that resulted in parts being out of spec. The mold steel dimensions were adjusted, 10 shots that met the specifications were sent to him, he accepted the mold and brought the mold over to his shop in the US. When he began molding parts with a process that the mold maker had given him he was unable to mold parts to spec and meet the required quality requirements. So what happened??
The failure lies in the fact that mold makers try to mold good parts during the first shots and/or make steel adjustments based on non-robust processes. The first step should always be find the a good robust molding process. The mold should first be adjusted for gate sizes, runner sizes, cavity balances, venting, pack pressure process windows, part sticking and so on. Once the mold is acceptable, a process with a wide process window must be defined and then the mold steel dimensions must be adjusted based on a robust process.
I follow a two-stage process that can be defined on this simple mold qualification diagram below. It is a pdf and so click and save it for the future if you like.
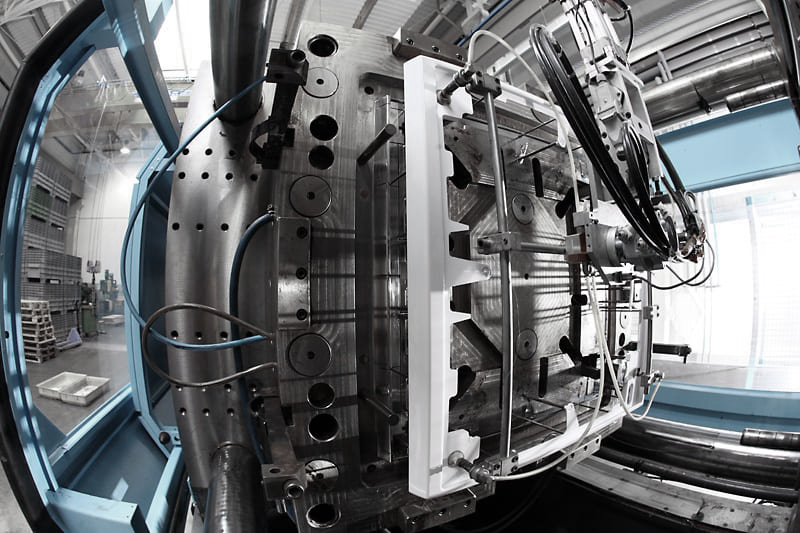