There are 11+2 molding parameters that make a difference in the quality of the part. Why the +2? The first phase is the Injection Phase where the cavity is filled with molten plastic. The second phase is called the compensation phase where the shrinkage is being compensated. The compensation phase is further divided into the pack and the hold phase. Most processors set only one number for the compensation pressure and time and call this as the holding phase. Not accurate, but it has become acceptable. So if you consider pack and hold as different phases then you end up with 13.
Following are the 13 molding parameters. These are machine inputs.
- Cooling Time
- Pack Pressure + Hold Pressure
- Pack Time + Hold Time
- Melt Temperature
- Injection Pressure
- Injection Speed (Velocity)
- Back Pressure
- Screw Rotation Speed
- Shot Size
- Transfer position
- Mold Temperatures
There are a few other parameters that are secondary parameters that do not get adjusted as often as the 13 mentioned in the previous section. They also do not have a substantial effect on the part quality.
- Decompression or Suck back position
- Pack Speed
Here are the machine outputs that should be monitored. Outputs are more important than the inputs.
- Actual Mold Temperature
- Fill Time
- Peak pressure during the fill
- Pressure at transfer
- Cushion Value
- Screw Rotation Time
- Cycle Time
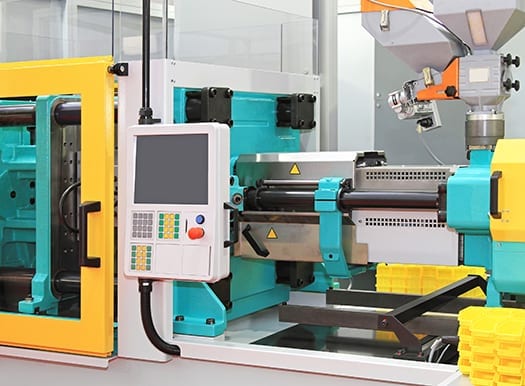