Maes Insights helps you get to your finished product smoothly. With years of experience in injection molding. From a 100+ well known companies Maes Insights delivers the perfect match in product designers, material suppliers, mold manufacturers and production facilities specifically for your product.
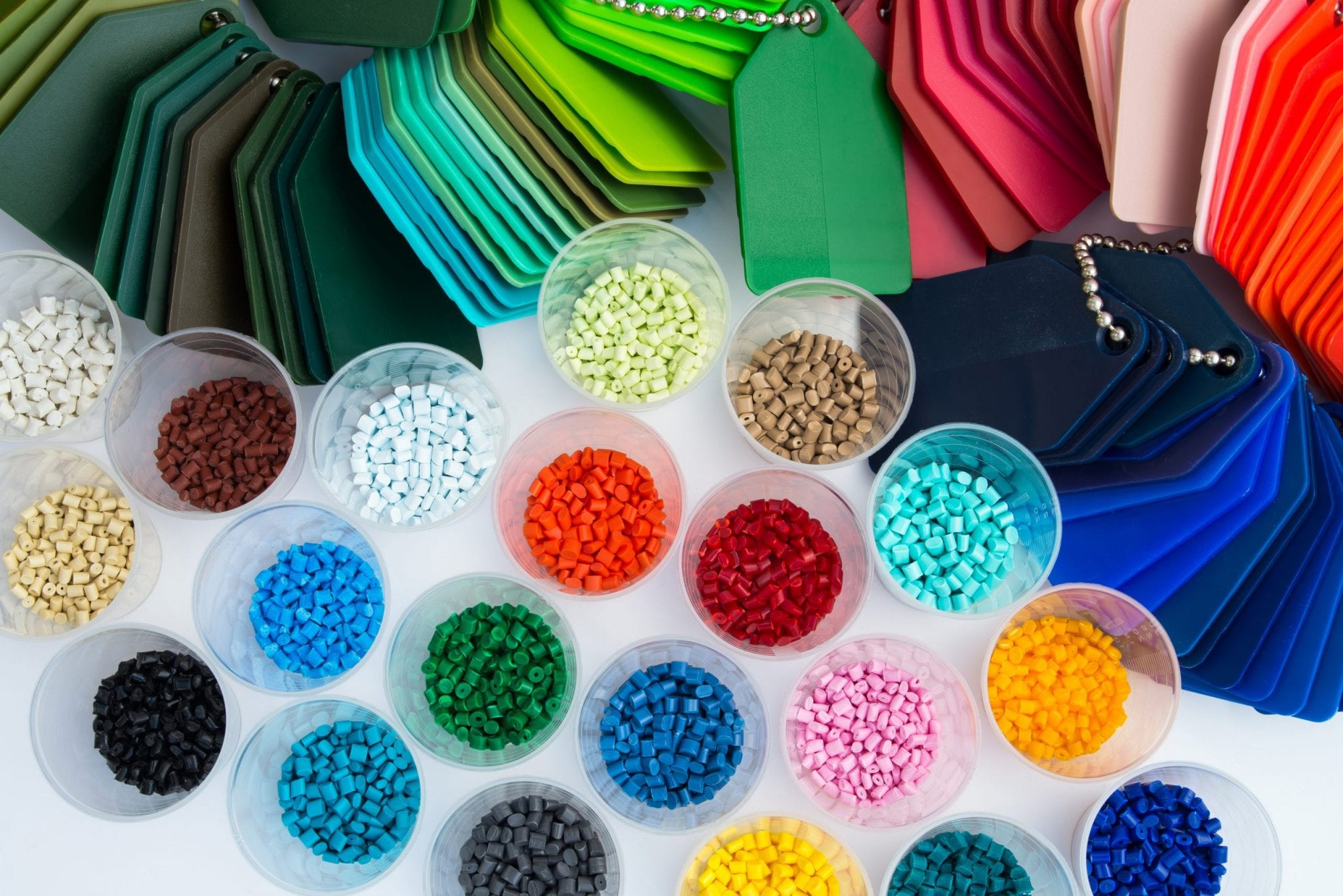
From idea to finished product
Supervising your injection molding process
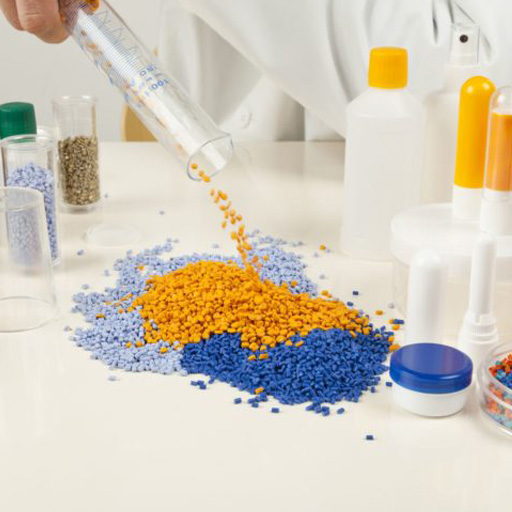
Research
Feasibility Check & Material research
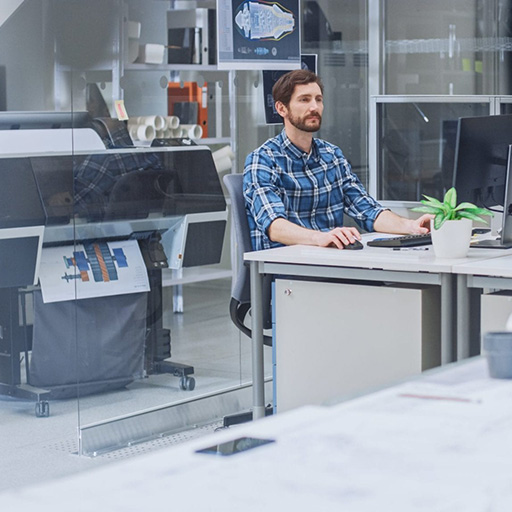
Development
Design, prototype & CAD modeling
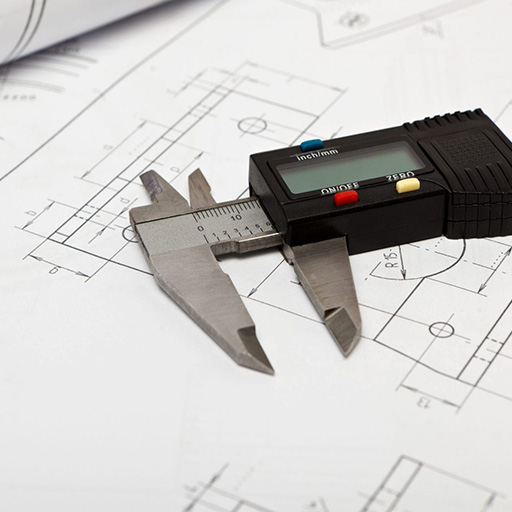
Verification & Validation
Testing & Measure
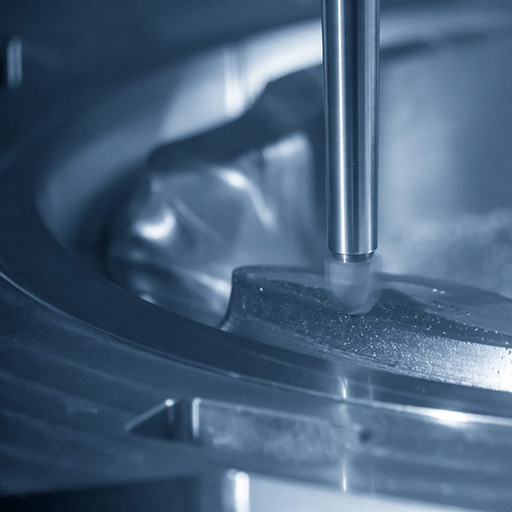
Realization
Molds & Tools
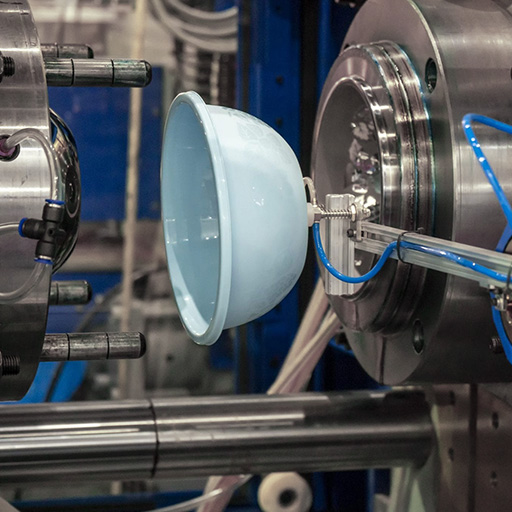
Production
1K, 2K & Cleanroom
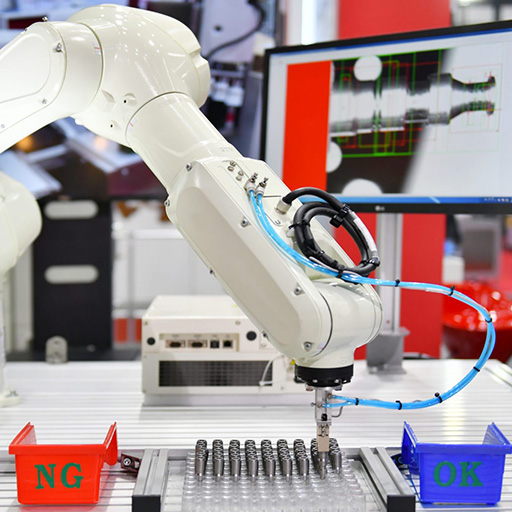
Assembly
Additional services, product quality & finish
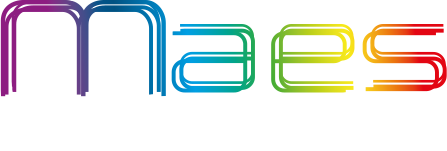
Would you like to optimize your injection molding process and save 30% or more?
Leave your details so that we can give you more information or schedule an appointment.
- Broad industry knowledge
- Large relationship network
- Your injection mold broker
- High support level
- High quality education level